Perusahaan manufaktur terkadang sering melakukan proses yang menyimpang dari tujuan yang sudah direncanakan. Padahal, kejadian tersebut bisa diminimalisir atau bahkan dihindari dengan menerapkan Material Requirement Planning atau MRP. MRP adalah sebuah sistem perencanaan yang dapat mengkontrol proses produksi dan distribusi semakin lebih baik pada perusahaan manufaktur atau pabrik. Sistem MRP sudah banyak diimplementasikan pada sebagian besar sektor perusahaan manufaktur dan produksi. Agar Ascomers tidak tertinggal dengan perusahaan kompetitor, yuk pelajari lebih lanjut mengenai sistem Material Requirement Planning dan bagaimana penerapannya pada blog berikut.
Apa Itu Material Requirement Planning?
Material Requirement Planning (MRP) merupakan sebuah sistem perencanaan dan pengendalian dalam manajemen rantai produksi (supply chain management) untuk mengelola persediaan mulai dari bahan baku, komponen, dan barang jadi dalam proses manufaktur atau produksi.
Sebelum menjalankan proses, MRP membutuhkan tiga komponen utama untuk membangun sistemnya. Tiga komponen tersebut yaitu master production schedule (MPS), bill of material, dan inventory master file. Perusahaan dapat memanfaatkan material requirement planning untuk memperkirakan jumlah bahan baku, menjaga tingkat persediaan, dan menjadwalkan produksi dan pengiriman.
Material Requirement Planning awalnya ditemukan oleh Joseph Orlicky dari J.I Case Company sekitar tahun 1960-an. Sampai saat ini, MRP sudah mengalami pengembangan hingga empat kali termasuk MRP I sesuai dengan tuntutan perkembangan teknologi dan tuntutan terhadap sistem perusahaan. Berikut ini perkembangan MRP mulai dari MRP I hingga MRP 9000.
- MRP I : Revolusi baru dalam manajemen supply chain terhadap komponen-komponen permintaan yang saling bergantung (dependent demand item). Termasuk unsur pengawasan dan pelaporan.
- MRP II : Pengembangan dari MRP I yang meliputi faktor tambahan seperti perencanaan jangka panjang, master scheduling, rough cut, capacity planning dan shop floor control.
- MRP III : Pengembangan dari MRP II dengan penambahan tingkat akurasi prediksi, permintaan, penggunaan secara tepat dan baik prediksi permintaan (forecast demand), sehingga dapat mengubah Master Production Schedule (MPS).
- MRP 9000 : Pengembangan MRP yang sudah menawarkan fitur yang lengkap dan terintegrasi dengan sistem management manufacturing, termasuk juga inventory, penjualan, perencanaan, pembuatan, dan pembelian menggunakan buku besar.
Dilihat dari MRP versi terbaru, sistem tersebut dapat diimplementasikan ke dalam software khusus dalam sistem Enterprise Resource Planning (ERP). Melalui adopsi MRP, perusahaan dapat meningkatkan efisiensi operasional, mengurangi biaya persediaan, dan meningkatkan ketepatan waktu dalam memenuhi permintaan pelanggan.
Manfaat Material Requirement Planning
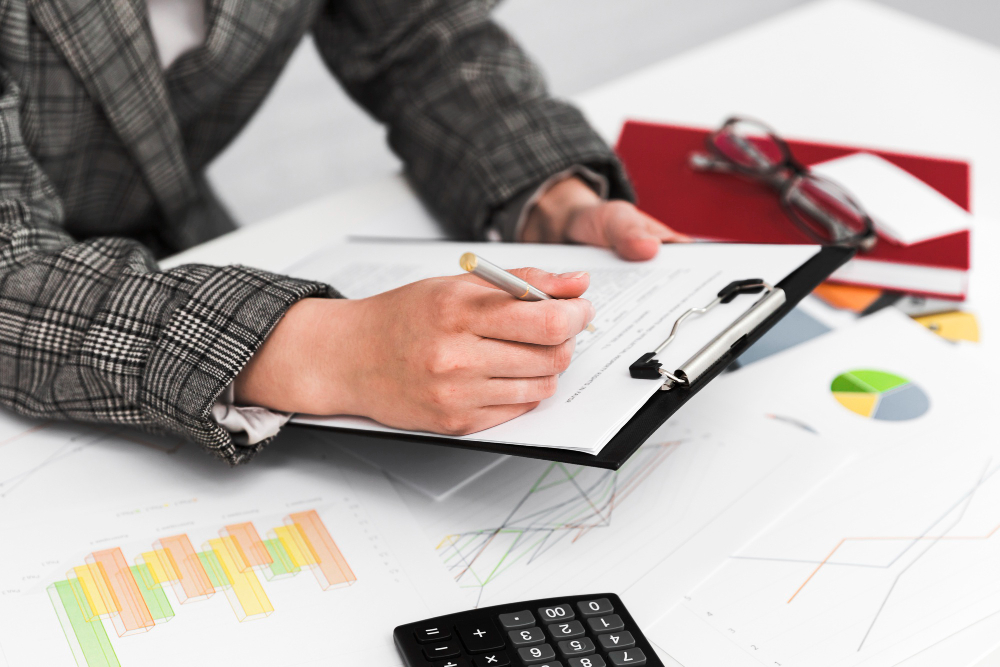
Ada banyak manfaat yang bisa dirasakan oleh pemilik perusahaan manufaktur atau produsen yang banyak menjalankan proses produksi setiap waktu. Berikut di antaranya :
- Merampingkan proses produksi.
- Mengoptimalkan biaya dalam satu produksi mulai dari biaya persediaan, pengelolaan, hingga biaya pengiriman.
- Mencegah terjadinya masalah dalam proses produksi dan merekomendasikan solusi untuk mengatasinya.
- Mengelola dan mengatur berbagai informasi yang berkaitan dengan proses produksi dan penyimpanan persediaan barang.
- Sistem MRP yang berjalan otomatis akan membantu efisiensi waktu produksi.
- Membantu mendokumentasikan data inventaris, pengiriman, transaksi dan arus kas dalam proses manufaktur.
- Membantu mengelola sumber daya dan bahan baku dalam satu periode.
- Menyajikan analisis data berbasis data historis sebagai pertimbangan evaluasi untuk perbaikan proses di periode selanjutnya.
Baca juga : Ketahui Inventory Control Untuk Memaksimalkan Bisnismu
Fungsi Material Requirement Planning
Sistem MRP pada dasarnya memiliki tiga fungsi utama, yakni sebagai sistem untuk kontrol tingkat persediaan, penugasan komponen berdasar prioritas, dan penentuan kebutuhan kapasitas (capacity requirement). Tanpa adanya ketiga fungsi tersebut, perusahaan memiliki visibilitas dan daya tanggap yang cukup terbatas, sehingga dapat menyebabkan :
- Pemesanan kebutuhan dan sumber daya yang terlalu berlebihan akan berakibat meningkatkannya biaya penyimpanan dan biaya produksi, atau
- Ketidakmampuan untuk memenuhi permintaan karena bahan baku yang tidak mencukupi, mengakibatkan hilangnya penjualan, kontrak yang dibatalkan, dan kehabisan stok.
- Dapat memberikan gangguan pada siklus produksi, penundaan proses produksi yang mengakibatkan peningkatan biaya produksi dan penurunan output.
Cara Kerja Material Requirement Planning
Sistem MRP dapat membantu bisnis dan produsen dalam menentukan apa yang dibutuhkan, berapa banyak yang dibutuhkan, dan kapan bahan dibutuhkan. Cara kerjanya adalah dengan mengubah perencanaan yang sudah dilakukan menjadi daftar persyaratan
MRP kemudian mengubah rencana menjadi daftar persyaratan untuk proses penggabungan, suku cadang, dan bahan baku yang dibutuhkan untuk menghasilkan produk akhir dalam jadwal yang sudah ditentukan. Lalu, cara kerja MRP lebih banyak berfokus pada penentuan struktur kegiatan produksi berjalan, menganalisis dan mengidentifikasi data, serta memantau dan membuat penyesuaian sesuai rencana yang sudah ditetapkan.
Dengan menggunakan MRP, Ascomers juga dapat menentukan kebutuhan sumber daya serta meningkatkan efisiensi produksi dengan memasukkan data ke dalam skema MRP seperti berikut :
- Item Name or Nomenclature : Penamaan akhir sebuah produk yang telah dihasilkan, biasanya disebut Level “0” di bill of material.
- Master Production Schedule (MPS) : Dokumen proses produksi yang memperlihatkan berapa banyak produksi yang diperlukan untuk memenuhi permintaan dan kapan itu dibutuhkan.
- Umur simpan bahan yang disimpan : Rentang waktu yang bisa produk lewatkan dalam gudang penyimpanan barang sebelum diproses dan didistribusikan.
- Inventory Status File (ISF) : Status bahan yang tersedia dalam stok dan bahan yang dipesan dari pemasok bahan baku.
- Bills of Material (BOM) : Rincian bahan dan komponen yang diperlukan untuk membuat setiap produk.
- Data perencanaan (Data Planning) : Dokumen perencaan yang menjelaskan terkait batasan dan aturan dalam proses produksi seperti perutean, standar tenaga kerja dan mesin, standar kualitas dan pengujian, dan teknik ukuran lot.
Prosedur dalam Material Requirement Planning
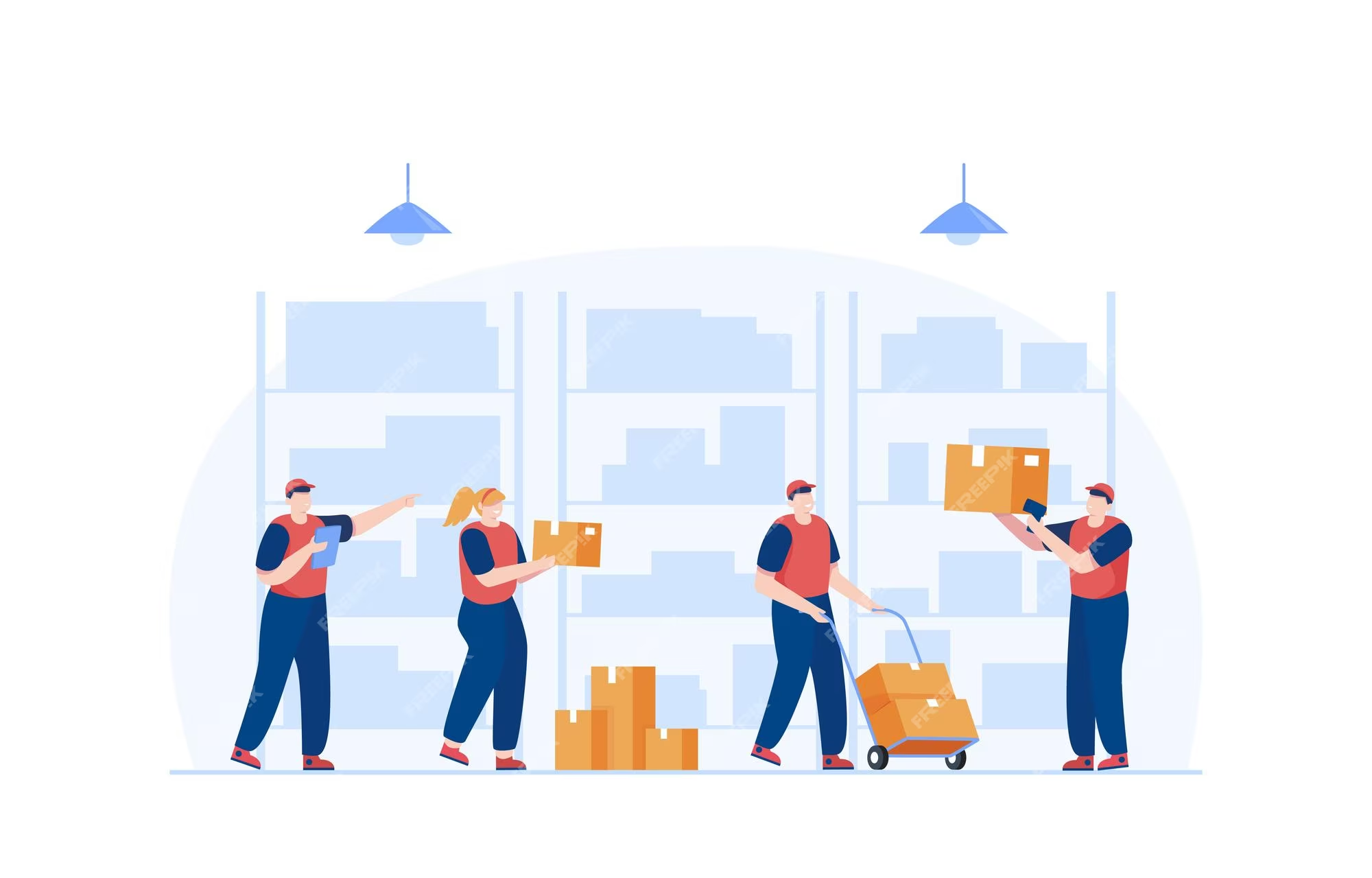
Umumnya terdapat 4 langkah penerapan MRP dalam pengelolaan inventaris ketersediaan barang, yaitu :
1. Mengidentifikasi Kebutuhan Untuk Memenuhi Permintaan
Langkah pertama dari proses MRP adalah mengidentifikasi permintaan pelanggan dan persyaratan yang diperlukan untuk memenuhinya. Dimulai dengan memasukkan pesanan pelanggan dan memprediksi penjualan (forecasting).
Melalui bill of material untuk kebutuhan produksi, MRP kemudian mengurai permintaan menjadi komponen-komponen individu dan bahan baku yang dibutuhkan untuk menyelesaikan proses produksi.
2. Memeriksa Inventaris dan Mengalokasikan Sumber Daya
Melakukan pemeriksaan inventaris kemudian mengalokasikan sumber daya yang sesuai untuk mengetahui dan memastikan aktivitas yang terjadi di dalam gudang atau ruang penyimpanan terkelola dengan baik.
Hal ini dapat memberikan Ascomers visibilitas dalam produk yang kamu miliki, lokasi keberadaannya, dan status prosesnya. Kemudian, melalui inventory master file yang sudah menyimpan riwayat aktivitas pengelolaan stok barang, sistem MRP akan membantu melakukan pemindahan ke lokasi yang lebih tepat dan secara langsung merekomendasikan secara otomatis pemesanan ulang.
3. Menjadwalkan Produksi
Dengan menggunakan master production schedule (MPS), sistem dapat menentukan berapa banyak waktu dan tenaga kerja yang diperlukan untuk menyelesaikan setiap langkah dari proses produksi dan waktu yang diperlukan agar produksi dapat berjalan tanpa penundaan.
Jadwal produksi juga mengidentifikasi mesin dan workstation apa saja yang diperlukan pada setiap langkah dan menghasilkan perintah kerja, pesanan pembelian, dan pesanan transfer yang sesuai.
4. Mengidentifikasi Masalah dan Membuat Rekomendasi
Sistem MRP dalam prosesnya dapat menghubungkan bahan baku dengan prosedur kerja dan pesanan pelanggan. Sehingga MRP dapat secara otomatis memberitahu Ascomers jika terdapat keterlambatan atau penundaan dalam proses produksi.
Kemudian, MRP dapat membuat rekomendasi aksi seperti secara otomatis memindahkan produksi masuk atau keluar, melakukan analisis lanjutan, dan membuat rencana pengecualian untuk menyelesaikan proses produksi yang diperlukan.
Baca juga : Mengenal Minimum Order Quantity (MOQ) Dalam Kegiatan Impor
AsiaCommerce Siap Membantu Manajemen Rantai Produksi Bisnismu
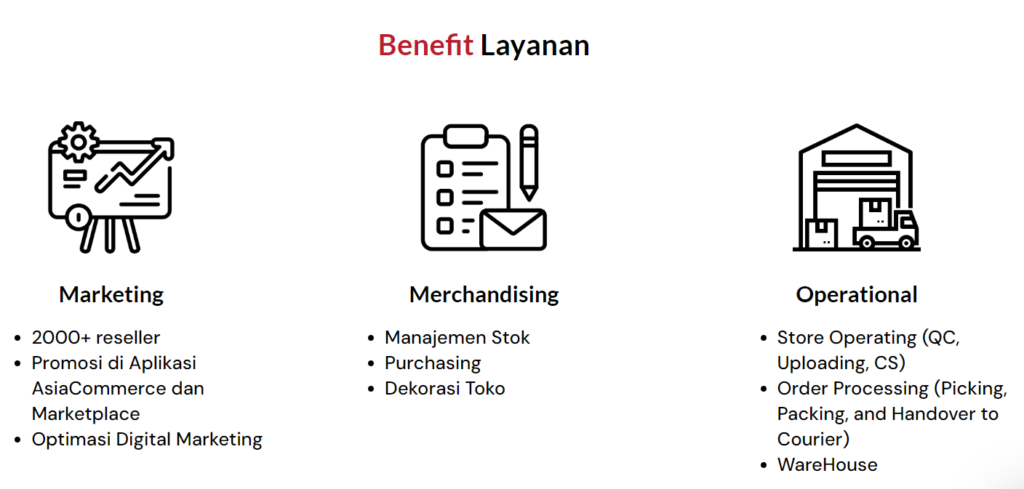
Jika Ascomers ingin memiliki supply chain management yang baik, AsiaCommerce siap membantu kamu mengelola produk yang dikirimkan ke pelanggan. Kami akan meningkatkan efektivitas strategi digital marketing bisnismu, memasarkan produk-produkmu ke ribuan reseller dan dropshipper yang akan membantu menjualkan produkmu, serta membantu memasarkan produkmu melalui berbagai marketplace terkemuka.
Tidak hanya itu, kami juga menyediakan layanan picking dan packing barang serta dukungan operasional toko dengan menyediakan tim operasional yang handal dan sudah profesional dalam mengelola produkmu dengan efisien.
Tunggu apa lagi? Klik di sini atau banner di bawah ini untuk segera memperluas jangkauan bisnis dan meraih keuntungan lebih besar bersama AsiaCommerce!
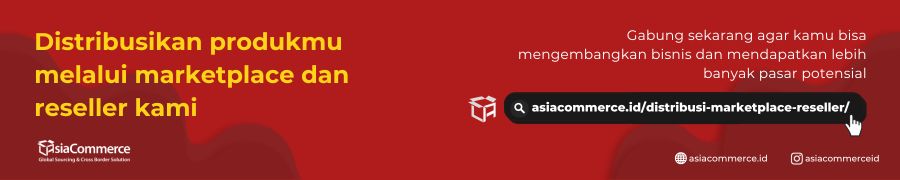